Digital Manufacturing: Revolutionizing Industry through Technology
In our rapidly evolving industrial landscape, the concept of “digital manufacturing” is gaining prominence as a transformative force. It signifies a fundamental shift in the way products are conceived, produced, and perfected. This article delves into the world of digital manufacturing, exploring its core principles, pivotal technologies, and its profound impact across various sectors.
Unveiling Digital Manufacturing
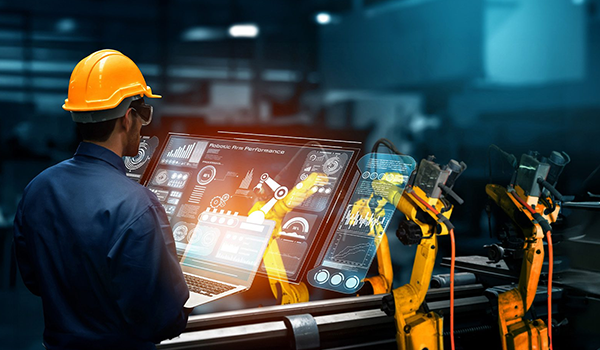
Digital manufacturing, often coined Industry 4.0 or the Fourth Industrial Revolution, represents a paradigm shift in manufacturing processes. At its essence, it entails the seamless integration of digital technologies into the entire manufacturing lifecycle, from product inception to production and post-production phases. The overarching objective is to create a harmonious and hyper-efficient system where data flows effortlessly throughout the product journey, empowering real-time decision-making and optimization.
The Cornerstones of Digital Manufacturing
DigitalDigital Twins: A central tenet in digital manufacturing is the notion of a “digital twin.” A digital twin is a virtual counterpart of a physical product, process, or system. It serves as an avenue to simulate and scrutinize the real-world behavior of systems within a digital realm. By perpetually generating and updating digital twins, companies gain profound insights into product and process performance, leading to refined decision-making and enhanced efficiency.
Interconnectivity: The bedrock of digital manufacturing is the interconnectivity of devices and systems, facilitated by the Internet of Things (IoT). Machinery, sensors, and ancillary components are connected to a network, enabling seamless data exchange and real-time sharing. This connectivity empowers manufacturers to remotely monitor and govern processes, whilst accumulating invaluable data for analytical purposes.
Data Analytics: The voluminous data churned out by interconnected devices is a veritable treasure trove of insights. Advanced data analytics, underpinned by machine learning and artificial intelligence (AI), are leveraged to decipher this data. Manufacturers can unearth patterns, prognosticate maintenance needs, refine production, and even tailor products based on individual customer inclinations.
Additive Manufacturing: Better known as 3D printing, additive manufacturing is a pivotal technological facet of digital manufacturing. It authorizes the creation of intricate, customized, and lightweight components with minimal material waste. Additive manufacturing has revolutionized prototype development, swift production, and even the creation of on-demand spare parts.
Key Technologies Steering Digital Manufacturing
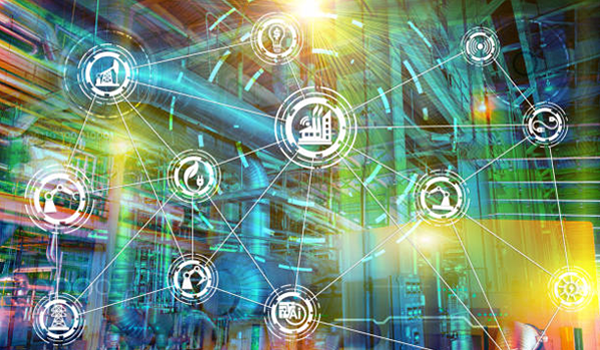
IoT and Sensing: The Internet of Things plays a pivotal role in the digital manufacturing arena. Embedded sensors in machinery and equipment amass data pertaining to variables like temperature, pressure, and humidity. This data is disseminated in real-time, enabling incessant monitoring and control of manufacturing operations.
Big Data and Analytics: The sheer volume of data engendered by IoT devices necessitates advanced data analytics. Robust big data technologies coupled with machine learning algorithms aid manufacturers in extracting actionable insights. Predictive maintenance, quality assurance, and demand projection are among the manifold applications.
Artificial Intelligence (AI): AI is the driving force behind the optimization of manufacturing processes, automated decision-making, and superior product design. Machine learning algorithms decode data and institute real-time enhancements to augment efficiency and product quality.
Cloud Computing: Cloud platforms facilitate the storage and processing of voluminous data. Manufacturers can access their data from any location, collaborate with remote teams, and harness cloud-based software for design, simulation, and other vital tasks.
3D Printing: Additive manufacturing’s sway stretches across diverse sectors, from aerospace to healthcare. 3D printing allows for agile prototyping, customization, and the fabrication of intricate structures that were hitherto implausible to manufacture.
The Impacts of Digital Manufacturing
Amplified Efficiency: Perhaps the most conspicuous boon of digital manufacturing is the elevation of efficiency. By optimizing operations through real-time data scrutiny, manufacturers can whittle down downtime, curtail waste, and augment overall productivity.
Bespoke Tailoring: Digital manufacturing ushers in an era of mass customization. Products can be finessed to align with individual customer preferences sans any detriment to production efficiency. This customization is particularly valuable in sectors such as fashion, automotive, and consumer electronics.
Cost Pruning: Through predictive maintenance and the curtailment of material waste, digital manufacturing can substantially slash operational expenditures. Companies can allocate resources more astutely and trim excess inventory.
Fostering Innovation: Digital manufacturing emboldens innovation by furnishing designers and engineers with advanced tools for product development. Agile prototyping and simulation expedite iterations and catalyze innovative designs.
Sustainability: Reduced material waste and energy consumption culminate in sustainability milestones. Additive manufacturing, for instance, can pare down the carbon footprint of production processes.
Supply Chain Streamlining: Digital manufacturing ushers in the era of real-time supply chain surveillance. Manufacturers can adjust production schedules and logistics in accordance with evolving demand, diminishing delays and refining overall supply chain efficacy.
Applications of Digital Manufacturing
Automotive Industry: The automotive sector has embraced digital manufacturing to streamline design and production processes. Digital twins facilitate vehicle design and performance enhancement, while 3D printing is deployed for custom component creation.
Aerospace: Aerospace manufacturers harness digital manufacturing to elevate aircraft and spacecraft performance. Digital twins are instrumental in predictive maintenance, culminating in downtime reduction and heightened safety.
Healthcare: In healthcare, digital manufacturing empowers the creation of custom medical devices and implants. Surgeons employ 3D-printed models for preoperative planning, resulting in superior patient outcomes.
Consumer Electronics: Consumer electronics companies are fervent adopters of digital manufacturing for rapid prototyping and customization. This paves the way for products tailored to individual user demands.
Energy: Digital manufacturing contributes to optimizing energy production and distribution. Sensors and data analytics underpin the monitoring and governance of energy systems, bolstering efficiency and curtailing waste.
Challenges and the Road Ahead
While digital manufacturing promises remarkable advantages, it is not devoid of challenges. Cybersecurity becomes a concern as more devices connect to the internet. Moreover, companies need to invest in workforce training to ensure employees are well-versed in digital tools.
The future trajectory of digital manufacturing is poised to incorporate heightened automation, more sophisticated AI applications, and the seamless integration of 3D printing into production lines. As technological advances continue, digital manufacturing will occupy an increasingly pivotal role in reshaping the industrial landscape.
In summation, digital manufacturing is engendering transformative waves by harnessing the might of data, connectivity, and cutting-edge technologies. Its repercussions are far-reaching – from augmenting efficiency and customization to pruning costs and galvanizing innovation. As companies progressively adopt and adapt to this digital revolution, the possibilities for advancement and expansion are virtually boundless.